多角度视觉走位设计是激光打标机在智能化、高精度加工领域的关键技术创新,其核心是通过多视角图像采集、三维信息重构与实时走位补偿的协同,解决传统打标中因工件定位误差、形状复杂或动态加工导致的精度不足、适应性差等问题。具体而言,其对性能的提升体现在以下五个核心维度:
传统激光打标机的视觉系统多为单角度(如顶部俯视),仅能获取工件的二维平面信息,难以应对曲面、倾斜面、阶梯面等复杂三维结构的定位需求。而多角度视觉走位设计通过以下方式提升精度:
-
三维信息重构,消除 “视觉盲区”
多角度视觉系统(通常配备 2-6 个不同角度的工业相机,如侧视、斜 45°、俯视等)从不同方位采集工件图像,结合立体视觉算法(如双目视觉、结构光扫描)重建工件的三维模型,精准还原其实际形状(如弧度、凸起、凹陷)。
- 例如:在曲面玻璃杯打标时,单角度视觉可能误判曲面为平面,导致打标图案变形;多角度视觉可计算每个打标点的法线方向,控制激光振镜动态调整聚焦深度和扫描角度,使光斑始终垂直于工件表面,图案失真率从传统的 5%-8% 降至 0.5% 以下。
-
动态偏差补偿,对抗定位误差
工件在输送或夹持过程中可能存在微小位移(如 ±0.5mm)、倾斜(如 ±3°)或变形(如薄片工件翘曲),多角度视觉可实时捕捉这些偏差(采样频率达 500-1000Hz),并通过运动控制算法(如 PID 实时调节)驱动激光头或工作台快速补偿走位(响应时间 < 10ms)。
- 应用案例:新能源电池极耳打标中,极耳薄(0.1-0.3mm)且易因张力变形,多角度视觉可识别其实际弯曲角度和位置偏移,确保激光打标在极耳中心区域,不良率从 3% 降至 0.1%。
传统激光打标依赖高精度夹具固定工件,对于不规则形状、多品种小批量的工件(如汽车异形零件、医疗器械组件),夹具定制成本高(单套夹具数千元)、换型时间长(1-2 小时)。多角度视觉走位设计通过 “无夹具定位” 突破这一限制:
-
特征点匹配,实现柔性定位
系统通过多角度摄像头捕捉工件的关键特征(如边缘、孔洞、纹理),与预设的 CAD 模型特征库进行匹配,自动识别工件的实际姿态(位置、角度、高度),无需依赖夹具的机械定位。
- 例如:在航空零件打标中,工件可能有多个不规则凸起,多角度视觉可识别每个凸起的相对位置,计算出打标区域的空间坐标,直接驱动激光头 “跟随” 工件形状走位,省去定制化夹具。
-
大范围视场覆盖,适配不同尺寸工件
多个摄像头通过拼接形成大视场(如 2m×1m),可同时处理大尺寸工件(如金属板材)或多个小工件(如手机按键阵列),无需分步移动打标,效率提升 50% 以上。
在流水线生产中(如饮料瓶日期打标、电子元件二维码打标),工件以 1-5m/s 的速度移动,传统静态视觉易因 “运动模糊” 导致定位偏差。多角度视觉走位设计通过动态追踪与预测算法解决这一问题:
-
多帧图像融合,消除运动模糊
不同角度的摄像头以高帧率(300-1000fps)拍摄移动中的工件,通过算法融合多帧图像,还原清晰的工件轮廓和特征点,避免因单帧模糊导致的定位错误。
- 应用场景:在罐头生产线,多角度视觉可清晰识别罐身的凹凸纹路,实时计算其旋转角度和移动速度,驱动激光头同步走位,确保生产日期打标在指定区域,偏移量 < 0.1mm。
-
轨迹预测,提前补偿滞后
系统根据工件的运动速度和方向,预测其未来 0.1-0.5 秒的位置,提前向激光振镜发送走位指令,补偿机械响应延迟(传统打标因延迟可能导致偏差 0.5-2mm)。
工业现场常存在反光、阴影、污渍等干扰(如金属表面反光、塑料件油污),单角度视觉易误判目标区域。多角度视觉通过 “交叉验证” 提升鲁棒性:
-
多视角信息互补,排除干扰区域
例如:金属工件打标时,某一角度的摄像头可能因强光反射无法识别打标区域,但另一角度(如 45° 斜拍)可避开反光,捕捉清晰轮廓。系统通过算法对比多视角图像,自动剔除反光、阴影区域的无效信息,确保特征点识别准确率 > 99.9%。
-
材质适应性增强
针对透明材质(如玻璃、塑料瓶),多角度视觉可通过不同波长的光源(可见光 + 红外)捕捉其内部结构或表面划痕,精准定位打标区域;针对深色材质(如碳纤维),则通过高对比度成像技术识别特征,避免 “漏打” 或 “错打”。
多角度视觉走位设计可与工业机器人、MES 系统无缝对接,实现全流程自动化:
- 机器人根据视觉定位结果抓取工件,激光打标机自动调整走位完成加工,无需人工对位,减少人力成本 30% 以上。
- 打标数据(如位置偏差、成功率)实时上传至 MES 系统,用于工艺优化和质量追溯,提升生产可控性。
多角度视觉走位设计通过三维精准定位、柔性适应复杂工件、动态追踪补偿、抗干扰强化四大核心能力,从 “精度、效率、适应性、自动化” 四个维度全面提升激光打标机的性能,尤其在 3C、汽车、医疗等高精度、高柔性需求的行业中,成为替代传统打标技术的关键升级方向。其本质是通过 “视觉感知 + 智能决策 + 精准执行” 的闭环,让激光打标机从 “被动按预设路径加工” 转变为 “主动适应工件实际状态加工”,大幅拓展了应用场景并提升了生产效能。
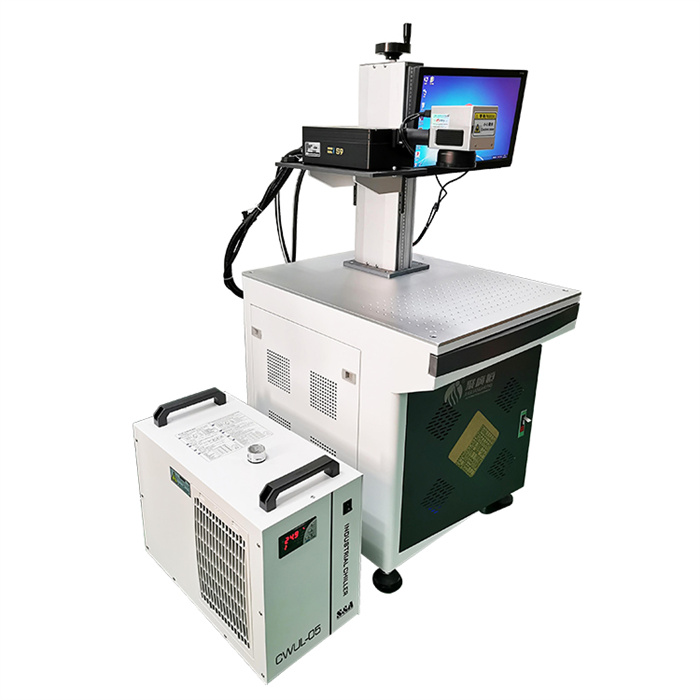
部分资料来源于网络,如有侵权,请与我们公司联系,电话:13580828702;